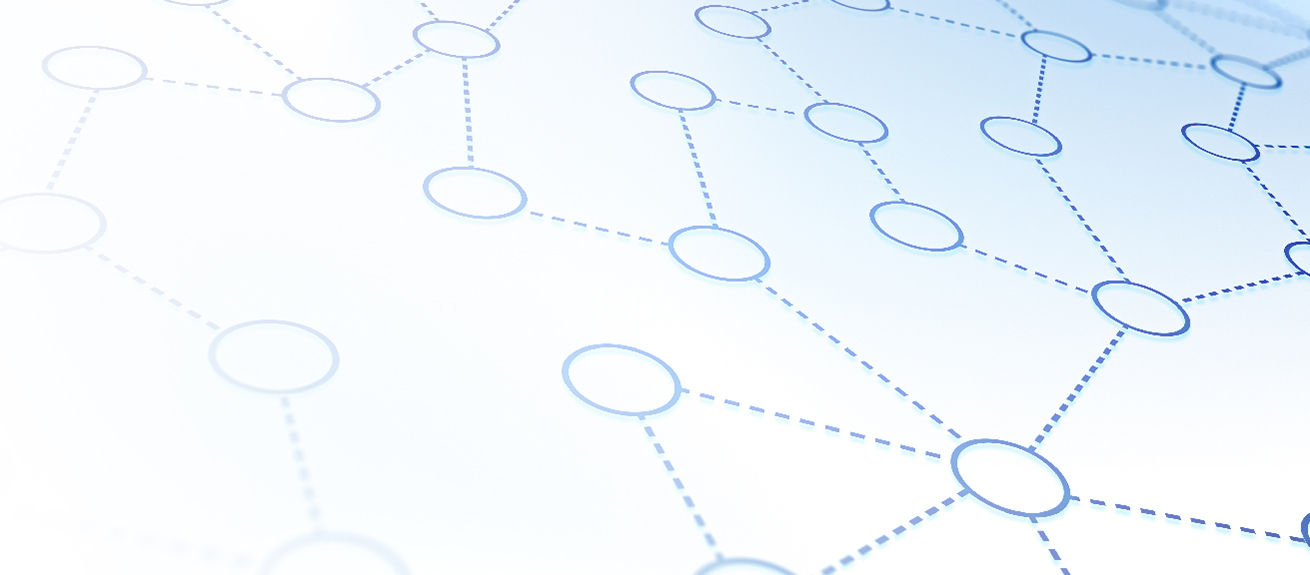
How crowdsourcing can make products better, cheaper and faster
It might sound foolish for an organization or company to outsource highly important projects, especially ones that are related to national security or matters at the heart of a business. But channeled right, the ideas of outsiders can provide fresh perspectives that may not come from seasoned in-house staff. It can be cheaper and faster too.
Here is an example from the United States military.
Amphibious tank project
DARPA, the US Defense Advanced Research Project Agency, decided to crowdsource its next-generation fighting vehicle: a tank capable of travelling in water and seamlessly continuing ashore, making it more secure for Marines to transition from sea to inland.
The risk involved in an exposed beachhead operation is so great that the Marines have not stormed a hostile beach since the Korean War. Steven Spielberg’s Saving Private Ryan, contains some of the most gruesome images of the Allied soldiers travelling through the deadly two-mile ship-to-shore range on Omaha beach with limbs being blown off and entrails spilling out. So the idea of developing an amphibious fighting vehicle has held sway among military experts for decades.
At the height of the debt-ceiling crisis in 2011, former defense secretary Robert Gates, under congressional pressure, promised to reign in the budget by saving 100 billion over the next five years, and in the process, was forced to shut down the amphibious vehicle project which had already cost the department 13 billion dollars over 20 years.
“The only entities able to contribute to the design of these important systems are corporations able to build multimillion dollar prototypes. That limits us to a handful of companies and maybe a few hundred brains,” said Army Lt. Col. Nathan Wiedenman, DARPA program manager pointing out the downside of over relying on just a few defense contractors, such as Lockheed Martin and Boeing. “In a nation of 300 million people, we can do better.”
In comes crowdsourcing
In October 2012, DARPA invited all American innovators to design a new amphibious infantry fighting vehicle—the Fast, Adaptable, Next-Generation Ground Vehicle (FANG). It called upon innovators of all stripes with expertise in designing and engineering drivetrain and mobility systems.
The goal was to build a vehicle capable of self-deploying from a home ship and delivering 17 Marines from a launch distance of at least 12 miles away from shore.
To run the competition, DARPA set up an online portal that served as a collaborative work system with the help of Vanderbilt University. “FANG applied a radical approach to the design and manufacture of a military ground vehicle while seeking to engage innovators outside of the traditional defense industry,” said Wiedenman.
The FANG challenge attracted more than 1,000 participants within 200 teams. On average, the 15 finalist teams spent about 1,200 hours of total time. Assuming a hypothetical hourly rate of $200 which would include administrative overhead, the collective design effort would have cost about $3.6 million, a grand bargain compared to the $1 million pre-tax payout.
And the winner is…
The winner turned out to be a three-person team dispersed across the US. The three, known as Team Ground Systems, was led by Eric Nees, his father James Nees, and their longtime friend Brian Eckerly.
Eric worked for a defense contractor in California, having done work on other ground vehicles. James, spent more than two decades working for the Air Force as a research engineer. And Brian went to high school with Eric, later graduated from Ohio State University with a bachelor’s degree in electrical and computer engineering. Only Eric had a strong background in automotive systems, putting him in the driver’s seat of the project.
Much like in the automotive industry, military vehicles are developed by teams organized around components and subsystems. Components are often designed as “black boxes,” namely, modular components, which will then be assembled into the final products. But the FANG project, making a tank be able to travel in water, was so innovative that it greatly tested the modular system because the interface to connect the separate parts had become too complex because of its new requirements.
While the design pulled together by Team Ground Systems relied almost entirely on existing components in the library, there was still significant work in spotting the right one. “We did select a lot of components from the repository, but so many times we had to go research individual components on the DARPA site to make sure that they were at least close to being compatible,” James said. “It’s nice to say you can just take all the LEGO blocks and stitch them together, but some components, though they look similar, are different. They just don’t work with the rest of the system.”
For Brian, his contribution to the team was largely focused on crunching simulation numbers. “I worked for two big banks,” Brian said. “I quit to pursue other interests—this competition being one of them.” He described the banking industry “was mostly data analysis and work on big data type projects”. “I was good at trying a lot of different combinations, collecting the data, and then providing the results back to my teammates on what was working well and what wasn’t,” he added.
Recipe for success
Team Ground Systems eventually settled with a design that traded automotive performance for manufacturing lead time by selecting components, including the main engine, that were available from the supply chain much faster compared to the other teams. A decisive factor for its victory, this winning strategy emerged only at the very end of the competition. But since the overall goal was to significantly speed up the design and manufacturing practice, Team Ground System was thus rewarded for speeding up manufacturing by a factor of two compared to the second- and third-ranked team.
“We really want to open the aperture to non-traditional design entities; folks who have the skills, but don’t traditionally have a mechanism by which they can participate in the development of military vehicles,” explained Nathan. “I can be a transmission engineer for a civilian firm who really knows my stuff, [and] I can log on, join and participate in a meaningful way.”
Eric seemed to agree. “It doesn’t take a lot of searching to see how this sort of crowdsourcing of design and integrated development environments have changed a lot of industries.” When asked how the money was divided, Eric laughed and said that there was only one fair way: A simple three-way split.
Howard Yu is Professor of Strategic Management and Innovation at IMD, where he teaches on the following programs: the EMBA, Advanced Management Program (AMP), Building on Talent (BOT), Breakthrough Program for Senior Executives (BPSE) and Orchestrating Winning Performance (OWP).
Research Information & Knowledge Hub for additional information on IMD publications
Research Information & Knowledge Hub for additional information on IMD publications
Research Information & Knowledge Hub for additional information on IMD publications
Research Information & Knowledge Hub for additional information on IMD publications
Research Information & Knowledge Hub for additional information on IMD publications
Research Information & Knowledge Hub for additional information on IMD publications
Research Information & Knowledge Hub for additional information on IMD publications
Research Information & Knowledge Hub for additional information on IMD publications
Research Information & Knowledge Hub for additional information on IMD publications
Research Information & Knowledge Hub for additional information on IMD publications
in I by IMD Brain Circuits 1 July 2025
Research Information & Knowledge Hub for additional information on IMD publications